Glenn Denomme, Vice President of Engineering, A123 Systems, Inc.
The success of the passenger electric vehicle industry relies heavily on reducing cost. Wide-spread consumer adoption of battery-electric vehicles (BEVs) and plug-in hybrid electric vehicles (PHEVs) is only a possibility when these cars offer both a competitive initial cost and lower total cost of ownership over the life of the vehicle. To sustain long-term cost-competitiveness, automakers and suppliers must focus on reducing manufacturing costs, starting with the lithium ion battery systems that power these vehicles.
The industry-wide standard for measuring battery costs is cost-per-kilowatt-hour (cost/kWh). However, while this will remain an important metric, there are other factors that contribute to the cost of lithium-ion systems that automakers must take into account when evaluating potential suppliers. One of the most critical, yet often overlooked, attributes that should be considered is how much usable energy a battery yields, which can have a significant impact on battery costs for BEV and PHEV applications.
Usable Energy 101
Often suppliers refer to a system’s “nameplate” or total energy when providing cost/kWh, but this can be deceiving since only a portion of the battery’s capacity can be used when a vehicle is in operation. Instead, automakers must consider their cost for the usable energy, which refers to the amount of a battery’s energy that can actually be utilized over the state-of-charge (SOC) range.
For passenger vehicles, batteries must be able to produce a certain amount of discharge (acceleration) and regenerative (braking) power over their lifetime, which translates into a pre-determined amount of usable energy necessary to meet these requirements. However, batteries have lower discharge power at low SOC and lower regenerative power at high SOC. To compensate, automakers must oversize the battery packs, deploying systems a nameplate energy that significantly exceeds the usable energy needed. This ensures that the battery can produce the necessary power and meet the energy and electric range requirements.
In addition to discharge and regenerative power capabilities, the automaker and battery supplier must choose a window of operation that will allow the battery to meet other requirements, including life and safety. Some battery chemistries are unable to be cycled deeply at high depths of discharge (DOD). By lowering the depth of cycling or DOD, it is possible to extend the battery’s cycle life.
However, while narrowing the window of operation allows for more cycles, it comes at the expense of using less of the battery. For example, manganese oxides experience degradation when fully charged or fully discharged, which impacts the life of the battery. This is due to chemical reactions in the cathode material (a phenomenon known as the Jahn-Teller distortion) or with the electrolyte (oxidation at high voltage.) Most battery chemistries have lower calendar life at high SOCs. By lowering the maximum SOC, it is also possible to extend the life of the battery by creating a more stable environment that is far less prone to damaging side-reactions.
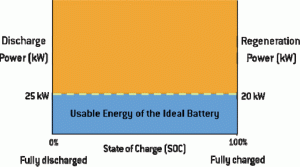
Abuse tolerance and concerns about safety may also limit the maximum state of charge of a battery. Most battery chemistries are more energetic at high SOCs, thus making them more prone to catastrophic failure, such as thermal runaway. One way to mitigate this potential issue is to not charge the battery as fully, which reduces the likelihood of the battery being involved in an overcharge situation that could result in a catastrophic failure.
In the example provided in Figure 1, the vehicle requires discharge power of 25 kW and regeneration power of 20 kW over the life of the vehicle, regardless of SOC, or how full the battery is. The ideal lithium ion battery system would be able to meet these power requirements at any given SOC, from 0 percent (empty) to 100 percent (full), and would have flat discharge and regeneration curves that follow the green dashed line. The blue shaded area represents the usable energy of this ideal battery, while the orange shaded area represents the battery’s power that remains unused because the electric motor is not designed to handle it. Having a battery with higher power than the motor can handle is not of value, other than to provide a cushion for eventual power loss over the life of the battery.
To ensure consistent vehicle performance and driver experience over time, automakers generally set battery power requirements that enable the discharge of the same power (or accelerate at the same rate) regardless of SOC. As previously noted, battery systems have lower power at low SOC, so typically, battery systems cannot sustain a high enough power output to meet this minimum discharge requirements at a lower SOC. In order to ensure consistent vehicle performance, a minimum SOC is established where the battery can meet the power requirements. At a higher SOC, as noted, automakers typically set a more conservative limit to address potential battery life and safety implications.
So, when evaluating potential lithium ion battery systems, automakers should look for batteries that retain their power capabilities over a wider range of SOC (as determined by the chemistry used to produce the battery), which allows for a smaller-capacity battery to be deployed to meet their usable energy requirements.
In addition, batteries inherently lose power capability over time, which reduces the amount of usable energy they yield because the range of SOC over which the battery can meet the power requirements becomes smaller. For example, a battery may initially meet the vehicle’s power requirements from 25 to 70 percent SOC, which means that roughly half of the battery’s energy is used during operation. Over time, as it loses power, the same battery may only be able to meet the vehicle’s power requirements from 30 to 70 percent SOC, which decreases its usable energy. Further, batteries in operation lose a portion of their total energy over time, which also reduces their usable energy. Therefore, automakers must consider degradation to ensure they are implementing batteries that yield their usable energy requirements throughout their lifetime. The alternative would be to replace the battery after a certain number of years, but this is costly and inefficient.
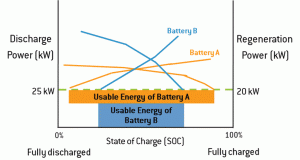
Figure 2 plots the discharge and regeneration power capabilities of two different battery systems over the complete range of SOC established in Figure 1. The usable energy of each battery is the range of SOC between the points where the discharge curve and the regeneration curve meet or exceed the vehicle’s power requirements. As illustrated, Battery A offers far greater usable energy than Battery B because it can sustain the discharge and regeneration requirements over a wider range of SOC and over a longer period of time. In this instance, Battery A is much closer to the ideal lithium ion system illustrated in Figure 1.
The Bottom Line: Why Usable Energy Matters
Understanding the concept of usable energy as a function of discharge and regeneration power over the range of SOC can help automakers determine the total cost of a lithium ion battery system over its lifetime. For example, it is reasonable to assume that 12 kWh of usable energy is necessary to maintain the discharge (25 kW) and regeneration (20 kW) power requirements over the life of a vehicle. To achieve this 12 kWh, a battery with greater total energy must be implemented to compensate for limitations at the lower and higher ends of the SOC range discussed previously.
However, the exact size of the battery needed is determined by the specific chemistry. Some lithium-ion systems offer greater usable energy, allowing automakers to implement a battery with lower nameplate energy, which reduces cost. Figure 3 charts the usable energy for Battery A and Battery B as a component of the batteries’ nameplate energy.
Because the usable energy of Battery B decreases as it loses power over time (as illustrated in Figure 2), the automaker is forced to implement a larger battery to achieve the 12 kWh of energy necessary to maintain the discharge and regeneration requirements (in this case, a 20 kWh battery is necessary because the battery’s chemistry yields 60 percent usable energy).
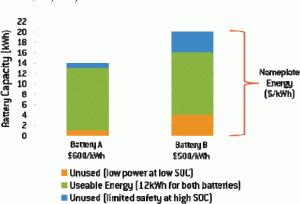
Conversely, Battery A maintains its power capabilities over a longer period of time, which increases its usable energy (in this case, about 86 percent of the battery’s nameplate energy can be used). As a result, an automaker can achieve the same 12 kWh energy requirement over a longer period of time by using a smaller-capacity battery (in this case, a 14 kWh system).
Using a cost-per-kilowatt-hour comparison for nameplate energy, Battery A is more cost-effective than Battery B:
• If Battery A costs $600/kWh, the automaker will pay $8,400 for the battery system ($600/kWh * 14 kWh battery = $8,400).
• If Battery B costs $500/kWh, the automaker will pay $10,000 ($500/kWh * 20 kWh battery = $10,000).
Expressed another way, automakers should consider cost/kWh for usable energy instead of cost/kWh of nameplate energy to determine the true cost of the lithium ion battery system. From the previous example, if the automaker requires 12 kWh of usable energy at the end of the battery’s life, then a 20 kWh battery using Battery B’s chemistry is necessary since it yields 60 percent usable energy. Conversely, since Battery A’s chemistry yields 86 percent usable energy, the automaker needs a system with 14 kWh of total energy to achieve the same 12 kWh usable energy requirement. This can be used to calculate cost/kWh for usable energy:
• If the nameplate cost of Battery A is $600/kWh, the total battery pack cost is $8,400. This translates to a cost of $700/kWh for usable energy ($8,400/12 kWh of usable energy).
• If the nameplate cost of Battery B is $500/kWh, the total battery pack cost is $10,000. This translates into a cost of about $833/kWh for usable energy ($10,000/12 kWh of usable energy).
So, although Battery B offers a lower cost/kWh for total energy, the steeper discharge and regeneration curves over SOC inherent to its chemistry force the automaker to deploy a system with greater nameplate energy in order to achieve its usable energy requirements. Battery A yields much higher usable energy, enabling the automaker to install a pack with smaller total energy, which is ultimately more cost-effective because the automaker is pay less per kWh for the energy the system will actually utilize.
Another benefit of implementing battery systems with greater usable energy is that vehicles are more fuel-efficient. If a battery can output the electric motor’s discharge power requirements at a lower SOC, the system has greater flexibility in allowable SOC range, allowing more opportunity to charge the battery with the regenerative braking mechanism. This enhanced fuel efficiency also contributes to a reduced overall cost for consumers.
Conclusion
A number of factors contribute to the cost of BEVs and PHEVs, but the lithium ion battery systems used to power these vehicles represents one of the best opportunities for cost reduction. As suppliers compete to reduce cost, relying solely on the cost-per-kilowatt-hour metric is often misleading when comparing BEV and PHEV batteries if the nameplate energy is used to make these cost calculations.
Instead, when determining which lithium ion battery systems to implement in their vehicles, automakers should consider usable energy as it relates to SOC and the requirements they set for discharge and regeneration power. Careful evaluation of a system’s usable energy will enable automakers to identify the most cost-effective, highest-value lithium-ion solutions to meet their vehicle requirements, ultimately helping to reduce the cost of electric drive vehicles for consumers and accelerate wide-spread adoption.
For more information, please contact A123 Systems, Inc. at www.a123systems.com.
This article was printed in the January/February 2012 issue of Battery Power magazine.