By Kent Griffith
January 17, 2022 | Battery engineers, scientists, investors, entrepreneurs, professors, analysts, consultants, CEOs, CTOs, CIOs, COOs, patent attorneys, business development managers, and sales managers gathered in San Diego—or joined online—for the Advanced Automotive Battery Conference in December 2021.
As the most expensive component of a lithium-ion battery, cathode materials are ripe for innovation. To set the stage, James Frith, BloombergNEF, opened the meeting with an overview of the Implications of Economy-Wide Decarbonization and a survey of the cathode landscape. According to BloombergNEF data, the cathode material mix in 2020 (across all sectors) was 46% lithium nickel manganese cobalt oxide (NMC, Li(Ni,Mn,Co)O2), 19% lithium cobalt oxide (LCO, LiCoO2), 18% lithium iron phosphate (LFP, LiFePO4), 16% lithium nickel cobalt aluminum oxide (NCA, Li(Ni,Co,Al)O2), and 1% lithium manganese oxide (LMO, LiMn2O4).
As we look toward 2030 and even 2040, BloombergNEF’s base projections show a sustained, dominant role for nickel-rich cathodes such as NMC, NCA, and variations such as lithium nickel manganese cobalt aluminum oxide (NMCA, Li(Ni,Mn,Co,Al)O2) and lithium nickel oxide (LNO, LiNiO2). It is worth noting that nickel-rich materials are converging toward a nickel content at which the varied nomenclature starts to lose significance; once nickel constitutes 95–98%, it may be simplest to consider all these phases as substituted LNO with substituent elements present on the order of 1% or less. The BloombergNEF base outlook also foresees a relatively constant fraction of approximately 20% LFP, a shrinking and almost vanishing contribution from LCO, and the arrival and substantial market penetration of some new contenders such as high-voltage lithium nickel manganese oxide (LNMO, LiNi0.5Mn1.5O4) and lithium-rich NMC materials. In an alternative scenario, BloombergNEF sees the potential for a more progressive chemistry mix, in which case they predict market domination by roughly equal proportions of lithium nickel phosphate (LNP, LiNiPO4), iron trifluoride (FeF3), and LFP in the next 20 to 30 years. In either case, metals like cobalt are projected to be phased out in favor of less costly, more widely available metals such as nickel and, ideally, iron and manganese.
Umicore, which produced enough cathode material in 2021 to power one million electric vehicles, is developing new materials for the advanced cathode sector. Rohan Gokhale of Umicore presented their cathode roadmap showing that materials with more than 80% nickel or nearly zero cobalt are already in the qualification and industrialization stage. On the horizon are manganese-rich electrodes with nearly zero cobalt, high-voltage spinels, and nickel- and cobalt-free cathodes. Both single-crystal and polycrystalline particle morphologies, and combinations thereof, are being explored. Umicore is also making cathode materials specifically tailored for use in solid-state batteries, which have their own specific requirements due to the solid-solid cathode-electrolyte interfaces. Customization of cathode particles for solid-state battery applications entails size and shape control and a homogeneous, conformal coating. Umicore saw a major year for production in 2021 with the opening of their first cathode active material plant outside Asia—a carbon-neutral facility located in Nysa, Poland.
CAMX has long been developing low-cobalt and high-nickel cathode materials, as detailed by company president and founder Kenan Sahin. For their approach to electrode powder stabilization, CAMX has focused since 2002 on grain boundary engineering, also known as crystallite surface engineering, in polycrystalline high nickel cathode materials such as NCA, NMC, and LNO. Sahin does not mince words when it comes to the trending phrase “cobalt-free” in the nickel-rich cathode ecosystem. “I am squarely opposed to [zero cobalt]. It’s not a viable pathway. In the United States alone, through recycling, we can get enough cobalt.” He continued, saying “There is plenty of cobalt if it is recycled and we can achieve tremendous advantages with just 5% cobalt, 3% cobalt, so why go to zero cobalt?” The GEMX cathode platform from CAMX features various classes of high nickel materials with cobalt-enriched grain boundaries and different stabilizing elements such as magnesium, aluminum, and manganese. Reported advantages for the cathode material manufacturing include low residual lithium, elimination of the need for water washing, and the ability to use lower grade lithium hydroxide precursors, which could be particularly important given the recent explosion in lithium prices. Minimizing residual lithium on the cathode powder surfaces is critical to avoid gas evolution and cell swelling or pressurization down the road. At the battery level, CAMX sees improvements in rate capability, accessible states-of-charge, cycle life, and low-temperature performance. Interested readers may follow the works on intra-granular cracking and cobalt-enriched grain boundary modifications (see Figure) that Sahin cited in his presentation, primarily from the groups of Jaephil Cho (Jaephil1, Jaephil2, Jaephil3) at Ulsan National Institute of Science and Technology and Eunseog Cho at the Samsung Advanced Institute of Technology (Eunseog1, Eunseog2, Eunseog3).
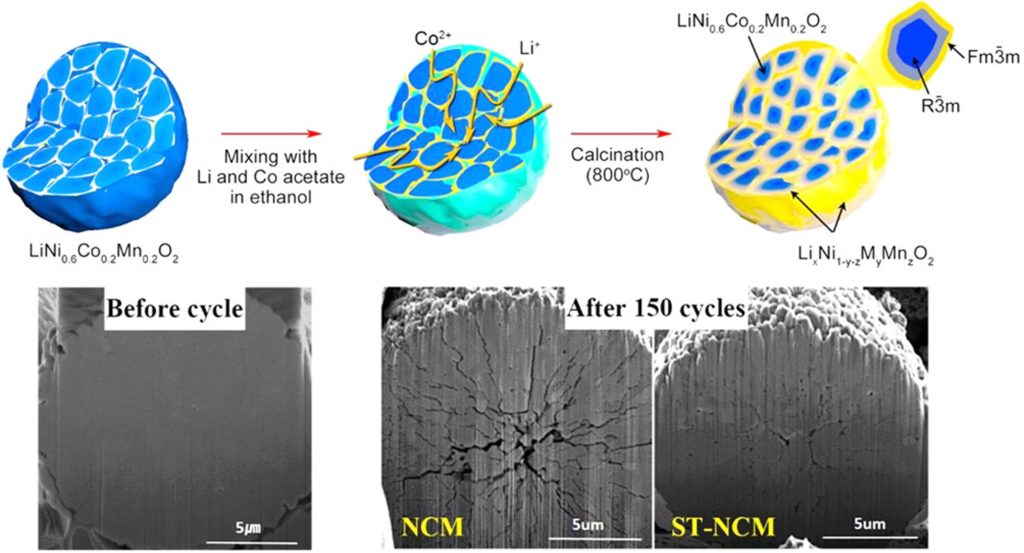
Reprinted with permission from Hyejung Kim, Min Gyu Kim, Hu Young Jeong, Haisol Nam, Jaephil Cho “A New Coating Method for Alleviating Surface Degradation of LiNi0.6Co0.2Mn0.2O2 Cathode Material: Nanoscale Surface Treatment of Primary Particles” Nano Lett. 2015, 15, 2111–2119. Copyright 2015 American Chemical Society.
Yang Shao-Horn, Massachusetts Institute of Technology, brought another perspective to high-energy cathode materials, that of stabilizing the cathode-electrolyte interface with improved electrolytes. A lithium-ion battery electrolyte, at least in a conventional liquid electrolyte cell, comprises a lithium salt and an organic liquid (solvent). The most common choices for salt and solvent are lithium hexafluorophosphate (LiPF6) and a mixture of alkyl carbonates such as ethylene carbonate (EC), dimethyl carbonate (DMC), ethylmethyl carbonate (EMC), diethyl carbonate (DEC), and propylene carbonate (PC). Shao-Horn’s team has shown that electrolyte breakdown occurs due to reactivity between carbonate liquids and state-of-the-art cathode materials such as NMC811, whereas no degradation of the carbonates was observed even under harsher conditions in the absence of the cathode material. In an effort to overcome this limitation, Shao-Horn and collaborators at MIT developed new electrolytes that present higher stability and can work with energy-dense lithium metal anodes paired with NMC and LMO or high-voltage LCO cathodes.
Representing the French institute CEA-LITEN, Sébastien Martinet covered topics from their laboratory ranging from active materials development to pilot manufacturing and abuse testing. On the cathode front, the institute has projects on lithium- and manganese-rich post-NMC materials with low cobalt, high-voltage spinel LNMO that is inherently free of cobalt and disordered rocksalt phases that are emerging as a next-generation candidate with higher energy density compared with existing materials. Disordered rocksalt cathode materials face challenges with rate capability, stability, and cyclability, and CEA-LITEN is working to overcome these challenges by incorporating fluorine as a dopant via ball milling, developing coatings, and exploring new lithium-rich compositions such as mixed sulfide-selenides (Li2TiSxSe3–x).