Contributed Commentary By Kate Johnson and Bruce Hilman, Dow Performance Silicones
August 17, 2018 | The market for plug-in hybrid and battery-powered electric vehicles (EVs) is on track to grow exponentially in the coming years, fueled by tumbling Lithium-ion battery prices, favorable government policies, and aggressive plans from automakers to ramp up production. Market research by Bloomberg New Energy Finance shows EV sales increasing from a record 1.1 million units worldwide in 2017 to 11 million units in 2025 and then surging to 30 million units in 2030.
Clearly, there is momentum behind the adoption of these vehicles. But enabling that growth as an industry and, more importantly, establishing a foothold as a competitor in this market will depend on the ability to meet consumer expectations for reliability, performance, and value. EV OEMs and their suppliers are in a constant race to bring better batteries to market.
The challenges to achieving this goal are numerous and complex. But, in very simple terms, advanced automotive battery-makers face two very basic issues—especially those developing lighter weight lithium-ion batteries vehicles. First, their next-generation automotive batteries must comply with large-volume, cost-effective assembly and production processes. Second, they must find innovative ways to manage the more intense heat generated from the higher energy densities these battery packs present. Keeping automotive battery cells at their optimum temperature ensures optimal performance and power.
The search for solutions to both of these challenges is driving new interest in silicone technologies, which are no stranger to the automotive industry or its most demanding underhood applications. Silicone adhesives, encapsulants, gasketing and thermal management solutions have already demonstrated decades of proven performance under the harshest automotive conditions. They are resistant to thermal shock, oxidation, moisture, and automotive fluids, and maintain their mechanical and chemical properties across operating temperatures from ‑40°C to 200°C.
Today, the versatile properties of the silicone molecule enable highly tunable performance attributes that are driving new innovations for streamlining assembly and enhancing the performance of advanced automotive batteries.
Formulation design builds on the intrinsic properties of bulk silicone, such as crystallinity, surface texture and environmental stability, and adapts the molecular architecture to achieve targeted performance attributes. This adaptation requires precisely controlled addition of other materials with close attention to their surface chemistry, passivation stability and the interfaces of each additive to the silicone backbone. This includes any treating agents used to control layer thickness, molecular selectivity and even interaction energetics within the matrix interphase. As additives become embedded along the molecular backbone they enable silicone formulations to deliver a wide array of final performance characteristics.
Flexible Processing, Consistent Performance
As a class of materials, silicones offer a wide range of handling and dispensing options for battery assembly operations, as well as an adaptable selection of flow, wetting, and adhesive properties.
Their lower viscosity and superior flow vs. urethanes, for example, offers benefits during processing and also translates into the ability to fully wet surfaces, which minimizes gaps and maximizes thermal contact between interfaces. The end result is more efficient dissipation of heat. Yet silicone adhesives, encapsulants, and gap fillers may also be formulated to not slump when dispensed onto vertical surfaces, and to stay put after shear of dispense is released.
Silicone solutions are also noted for their simplicity during processing. Battery-makers most commonly rely on room-temperature vulcanizate (RTV) formulations that offer the option to accelerate cure with the application of heat for increased productivity. Notably, post-cure properties of silicones are not significantly affected by temperature-accelerated cure, another benefit that distinguishes them from organic solutions.
RTV adhesives are generally favored for automotive-scale battery packs due both to their relative size as well as the limited high-temperature stability of lithium ion cells, which makes the use of ovens problematic. However, recent advances in curing system technology have enabled faster curing times without the use of heat, which can substantially improve throughput and reduce cycle times for high volume production.
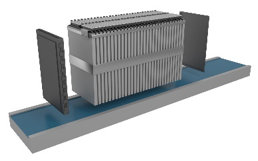
Recent innovations at Dow Chemical, for example, introduced a thermal radical cure adhesive technology that cures in half the time as conventional heat-cured, platinum-catalyzed silicone systems. Other recent advances from the company have driven a growing portfolio of hot melt adhesives, which are a special class of reactive, neutral cure silicones that dispense easily as a liquid melt and cure quickly at room temperature to form a viscoelastic polymer that provides strong, flexible, primerless adhesion to common plastic and metal substrates.
In short, silicone technology enables battery-makers to choose the right balance between accelerating or simplifying their processing operations. The molecular chemistry of silicones also enables many paths toward tailored and uniformly reliable performance.
The end result again is broad latitudes for battery designer and manufacturer seeking to optimize the performance profile of their products.
Reducing Stress
The emergence today of more compact, high-energy-density battery designs is also introducing new thermal management challenges. Silicones are more thermally stable at temperatures above 125°C compared to organic polymers, such as epoxies and urethanes. While this quality is more relevant for automotive electronics than lithium-ion batteries, where the chemistry can become volatile at higher temperatures, the high thermal stability of silicones makes them a strong candidate for managing heat, insulating components, and isolating thermal events in and around automotive battery designs.
Epoxies, or carbon-based polymers, have an advantage of providing structural strength and rigidity, giving them an edge in interfaces that require great bonding strength without fasteners. Similarly, joints designed to allow very little movement during thermal cycling, vibration or other application stress may benefit by the high modulus and durometer hardness of epoxies. With those characteristics, however, comes tremendous stress that can be produced during any induced movement. During thermal cycling, bonded surfaces that exhibit a significant mismatch in their coefficients of thermal expansion (CTE) can easily lead to wire or component breakage.
Depending on formulation, silicones offer a very tunable modulus, allowing them to cure into very hard materials or, alternatively, into very soft gels that can protect components while imposing minimal stress. In general, even high-modulus silicones do not share the mechanical strength of epoxies, and tend to be softer and highly flexible. Although their CTE is not significantly different, their very low modulus typically compensates for this during thermal cycling.
Consequently, silicones tend to put much lower stress on components. Even highly filled thermally conductive silicone adhesives still have very low moduli in comparison with similarly filled epoxies. Furthermore, very soft silicone gels have been measured with an order of magnitude lower expansion pressure, which provides gentle cushioning to sensitive components.
While soft gap fillers, encapsulants and pads can generate some stress during thermal cycling, this stress is typically lower than what alternate materials impose and often can be managed through design.
The tunability of silicones applies to properties other than modulus, such as flexibility and elongation at break. Silicones may either be formulated to insulate sensitive battery components from heat and vibration, or to conduct heat away. They may also be foamed in place to enable lightweight seals and gaskets. Or they may be designed to provide a barrier to isolate thermal events, contributing a higher degree of safety to battery designs.
Applications by battery type
Advanced automotive battery cells appear in several formats today:
Cylindrical cells are the most common cell type in the battery industry. They are broadly used in specific well-known electric vehicle applications, and support the use of more efficient, automated assembly processes that deliver consistent performance.
Prismatic cells are an increasingly popular alternative to cylindrical cells as their energy density offers performance improvements, while their shape simplifies the task of connecting cells together into battery packs. Due to the higher energy density, sufficient thermal management is critical to manage the performance of these cell types.
Pouch cells, comprising thinly separated pouches, require additional process steps for assembly due to their lack of rigidity. In return, they are able to deliver high specific energy and application-specific customization.
These multivariate forms further complicate the materials selection process for adhesive, encapsulant, and thermal management materials. Yet here again, the versatility of the silicone molecule offers flexible options for both assembly and performance enhancement.
Silicone adhesives, for example, offer a lightweight, simpler-to-assemble alternative to mechanical fasteners for cylindrical and prismatic battery modules and packs. Similarly, silicone coatings, encapsulants and foams offer lightweight protection, thermal management and thermal event isolation for electronic control units and individual modules in all battery categories. Here too, the ability of these silicone formats to avoid slump and hold their shape after dispensed helps ensure cells of all types move efficiently forward on the line.
Lastly, and perhaps of greatest interest to battery designers, are high-flow silicone gap fillers, which are well-suited to fully fill difficult to reach gaps and flow into the challenging geometries of various battery designs to optimize thermal transfer.
Despite two decades of impressive applications and achievement, EV battery technology is still a frontier for cutting-edge concepts that must be road-tested in a very competitive market. While silicones are a much more familiar and proven technology in the automotive industry, the intrinsic versatility of these materials continues to fuel new innovations in assembly, protection and thermal management. The practical benefit for advanced battery manufacturers is a broad and growing toolbox of highly flexible solutions for many of today’s most challenging battery pack designs and applications.
Kate Johnson is global technical leader for Automotive Electronics at Dow Chemical, where she conducts technical development in North America, manages key customer accounts and leads commercialization of new technologies. Kate has received two R&D 100 awards and has been recognized by the Society of Automotive Engineers for presentation excellence at the industry group’s World Congress. She has also served as president of the Society of Women Engineers. She can be reached at kate.johnson@dowcorning.com.
Bruce Hilman is global strategic marketing leader at Dow Chemical for the transportation assembly market segment, which supports many emerging trends including autonomous driving and electric vehicles. Bruce has broad ranging technical and commercial leadership experience delivering innovative materials to other growing industries including solar, LED lighting, consumer electronics, and power electronics. He can be reached at bruce.hilman@dowcorning.com.