By Kent Griffith
November 19, 2019 | SEOUL–While only 2% of the cars on the road are electric, the cumulative energy stored in EV batteries has already surpassed all other lithium-ion battery applications combined. It is no wonder then that all major battery manufacturers are looking toward the future through the lens of EVs. With the shift toward automotive applications, there are increasing demands on lithium-ion battery performance. In order to alleviate range anxiety, the energy density must increase. In order to approach the refueling experience of fossil fuel vehicles, the charging time must be shortened. However, safety is critical, and performance advantages must not compromise safety.
Last week, the International Conference for Advanced Cathodes gathered top scientists and engineers from around the world for a three-day meeting in Seoul, South Korea, to address these complex issues. Battery manufacturers, academic researchers, and representatives from national laboratories gathered to share their latest discoveries and future directions.
It is abundantly clear that the future of high energy batteries will converge on layered oxides increasingly rich in nickel. The reasons are multifold. Early lithium-ion batteries comprised a cathode of lithium cobalt oxide [LiCoO2] and an anode of graphitic carbon. Cobalt can be replaced by other metals such as manganese, nickel, and aluminum. This has led to the development of the NMC [Li(Ni,Mn,Co)O2] and NCA [Li(Ni,Co,Al)O2] cathodes used in electric vehicles today. Both manganese and aluminum are essentially inactive, acting as stabilizing agents to increase safety properties and the number of charge/discharge cycles the battery can achieve.
However, as the nickel content increases, the amount of lithium that can be cycled in and out of the cathode increases and the energy density goes up. Moving to nickel-rich cathodes also eliminates the need for cobalt. Cobalt production is marred by ethical issues surrounding mining practices in the DR Congo, which supplies about 50% of the cobalt ore. The cobalt price is also extremely volatile, and the sustainability of this element is questionable. On the other hand, nickel is more widely distributed geographically and produced at much larger quantities. Its price is buffered by large steel and alloy markets. State-of-the-art commercial cathodes already contain up to 80% nickel (metal-site basis) with formulations such as the NCA from Panasonic and Tesla or NMC811 from many others. However, nickel-rich cathodes face challenges in cycling stability and in thermal stability, which mean that they require innovations to last the 10+ years required for automotive applications or meet national and international safety requirements.
At the International Conference for Advanced Cathodes, organized and hosted by Professor Yang-Kook Sun, Hanyang University, a number of strategies were presented in an effort to overcome these challenges. Professor Sun’s own research has shown that the most important degradation mechanism of nickel-rich cathodes is from particle cracking at the interface of primary particles within larger secondary particles (Figure 1; DOI: 10.1021/acsami.9b09754).
This cracking along the grain boundaries occurs due to a large strain that occurs when most of the lithium is removed from the cathode during charging. Dr. Hyungsub Kim of the Korea Atomic Energy Research Institute (KAERI) studied an NMC with 90% nickel and used an advanced characterization technique called neutron diffraction to determine that a known defect–Li/Ni disorder–actually decreases as the nickel content increases; however, it must be measured after cycling the cathodes because it increases significantly from the originally-prepared material. Dr. Kim also showed that nickel will dissolve when the cathode is overcharged to a high voltage of 4.9 V, which leads to a loss of capacity.
Counterintuitively, this overcharging is actually beneficial for the problem of voltage decay, because it dissolves the passivating surface layers such as nickel oxides. From another national laboratory, Dr. Jun Liu of Pacific Northwest National Laboratory in Washington presented results from 2019 Nobel Prize winner Prof. Stan Whittingham showing that niobium is an effective doping and coating agent to minimize capacity fading and increase stability in nickel-rich cathodes (DOI: 10.1021/acsami.9b09696).
Professor Won-Sub Yoon of Sungkyunkwan University in Seoul presented a surprising result: when cobalt content is fixed, increasing nickel at the expense of manganese actually increases the lithium-ion diffusion, decreases the number of defects, and decreases the strain induced during charging (DOI: 10.1002/aenm.201701788).
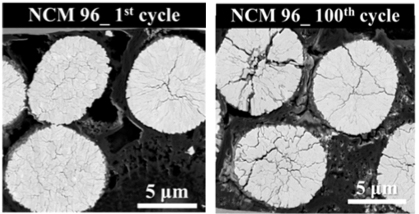
Industry Futures
As a sign of the importance of and progress in nickel-rich cathodes, major industry players such as BASF, LG Chem, and EcoProBM presented their latest results in this area as well as outlining future plans. BASF made a stake to the claim of world-leader in NCA energy density for EV applications. They plan to commercialize NCA with 90+% nickel, and NMC versions with 80%, 85%, and 90% nickel in the near future. One particularly interesting pre-pilot-scale project within BASF is atomic layer deposition coating of advanced cathodes, a method that has long been known to benefit performance but was assumed to be unscalable or at least economically unfeasible. However, BASF recently switched from a batch process to a continuous process and claims to have achieved a 100x boost in throughput to 750 tons per year. Finally, BASF observed that the choice between NCA and NMC is coming down to customer history and preference as the nickel content increases and the properties converge.
EcoProBM is an interesting player in this sector because they exclusively sell cathodes with at least 80% nickel and have even commercialized 90% nickel materials. They expect to supply about 50% of the 37,000-ton demand for high-nickel cathodes in 2019. LG Chem revealed that the global EV market is growing faster than expected and their new estimates for 2020 are double what they had predicted back in 2016. Partnering with POSCO Chemical for their cathode raw materials, LG Chem manufactures batteries for 26 electric vehicle models. The ‘Gen. 2’ material is NMC622 with 60% nickel, but much like the competition, they plan a nickel-rich NMC for their upcoming ‘Gen. 3’ product. LG Chem is pursuing an undisclosed doping and coating strategy for the high-nickel NMC along with a new anode formulation, non-flammable separator, and electrolyte additives to reach their cell performance targets of 670 Wh/l and 295 Wh/kg.
Looking toward the future, Dr. Wangmo Jung of LG Chem noted that EVs will not simply replace conventional vehicles but offer a new, fun driving experience with a low center-of-gravity and rapid acceleration while also serving as the best platform for autonomous driving.
While nickel-rich cathodes were the focus, several next-generation technologies were also discussed. If we are to move beyond the energy limits of the present technology, which is rapidly approaching its theoretical limit, a new cathode material is required. Professor Naoaki Yabuuchi of Yokohama National University is a leader in the field of cathode materials known as lithium-rich disordered-rocksalt compounds. He demonstrated capacities 50-100% higher than Ni-rich materials in Li-rich phases, though further work is needed to improve the cycle life of these new cathode candidates (DOI: 10.1002/tcr.201800089).