March 9, 2018, | News Brief | Sugar may not be good for your health, but the wrinkle it provides to researchers could be great for the future of battery technology. Scientists at Rice University and Arizona State University got a bit of sweet satisfaction from their solution to a long-standing conundrum: the formation of dendrites that degrade and ultimately destroy lithium metal batteries. The team uses sugar cubes as a key component in building dendrite-quenching substrates for lithium anodes.
Lithium, a soft metal, has the ability to store far more energy than current electrodes used in lithium-ion batteries. It could allow electric cars to run longer on a single charge and facilitate backup energy supplies for solar power grids. But pure lithium is highly reactive with organic battery components, and researchers are looking for ways to make lithium batteries as long-lasting and safe as lithium-ion batteries.
A process that begins with combining sugar and a liquid polymer known as PDMS winds up as a sponge-like substrate that helps dampen the growth of dendrites in lithium metal batteries. The project by scientists at Arizona State University and Rice University detailed the likely cause of dendrites that can cause short circuits in lithium metal batteries. Courtesy of Arizona State University
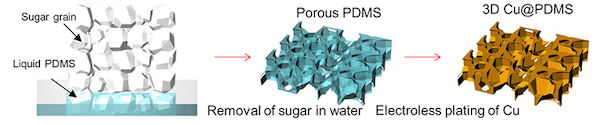
The collaborative team led by Hanqing Jiang, a professor at the School for Engineering of Matter, Transport and Energy at Arizona State, reported that stress within a lithium anode can prompt the formation of dendrites, just like the “whiskers” often seen in stressed tin and zinc coatings, and ultimately cause batteries to fail. Dendrites growing from an anode consume both lithium and the electrolyte and can short-circuit the battery.
“There are two points worth noting in this paper,” said Rice materials scientist and co-author Ming Tang. “The first is that we proposed a fundamental mechanism for lithium dendrite growth, and the second, based on that understanding, is a technology to help suppress it.”
Tang, former Rice postdoctoral researcher Liang Hong and Rice graduate student Fan Wang modeled the compressive stress generated during the plating of soft metals on flat surfaces to show how lithium dendrites grow.
“Whiskers or needle-like protrusions forming on metal surfaces under stress are a long-known phenomenon in metallurgy,” Tang said. “People have noticed that dendrites in lithium are similar to the whiskers in tin and zinc, but they haven’t known that compressive stress exists in lithium metal during battery cycling. The experiments by Dr. Jiang’s group provided definitive confirmation of the association between compressive stress and dendrite formation.”
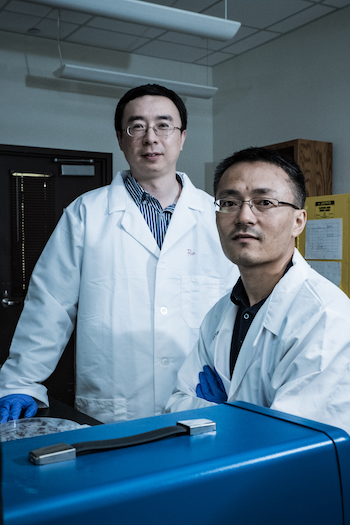
Tin whiskers are like straight wires, but lithium dendrite filaments take a more meandering path. Tang said the research suggests the mechanism for the two is similar. “Compared with tin, lithium has an even lower melting point at 180 degrees Celsius (356°F),” he said. “This means lithium atoms are even more mobile at room temperature. If there’s stress, the atoms are very happy to move. That’s why we can see dendrites form within hours, even minutes.”
The Rice team’s theory explains the experimental observations made by Jiang’s lab, which showed that plating lithium metal onto a flat substrate offered it nowhere to go but out in the form of dendrites.
To solve this problem, the team looked for a way to direct stress inward by electroplating lithium around a soft, porous substrate that would allow for breathing room and quench dendrite formation.
This is where the sugar comes in. To make test batteries, the Arizona State lab infused sugar cubes with liquid silicone and then dissolved the sugar, which left behind a three-dimensional porous structure of soft silicone.
“It’s really cool,” Tang said. “The sugar becomes a sacrificial template. When it’s removed, it leaves a substrate with a very large internal surface, like a sponge that can collapse and deform.”
The Arizona State lab built lithium metal batteries with a thin copper film within the soft substrate to conduct electrons. The batteries had a coulombic efficiency, the ability to maintain energy density, of nearly 98 percent over 200 cycles and easily outperformed test cells with flat copper substrates.
The substrate showed the ability to wrinkle under stress and make room for the invading lithium. “There were remarkable reductions in dendrite growth,” Jiang said.
In ongoing research, the batteries will be tweaked and tested to see how they hold up over the long term, Tang said. “For practical purposes, you want batteries that last for several thousand cycles so they will last for years,” he said. “That needs to be looked at.”
Co-authors of the paper are graduate students Xu Wang, Wenwen Xu and Haokai Yang and visiting scholar Wei Zeng at Arizona State and Professor Huigao Duan at Hunan University, China.
The Department of Energy Office of Science supported the research. Computing resources were provided by Rice University through the Big-Data Private-Cloud Research Cyberinfrastructure funded by the National Science Foundation.