Contributed Commentary By Brian Morin, Soteria
August 13, 2018 | Last year I found myself with a dramatic improvement to battery architecture—and a market dead end. But necessity is the mother of invention, and much discussion led to a key discovery about the market. The Soteria Battery Innovation Group was born as much from a technological advance as a cultural revelation. And now it’s poised to bring about big changes in lithium ion batteries.
In late 2016, I was president and co-founder of Dreamweaver International, developing nanofiber-based separators. Both I and one of our long-time customers, Nanonouvelle Pty, were beginning a process to raise money to help launch our products into the battery market. I often commiserated with my counterpart there, CEO Stephanie Moroz, about how difficult the process was. Even in the face of fantastic technical results from both companies, potential venture capital and other funding agents were unduly conservative, in our eyes.
For several years, Stephanie’s company had been using our separators as a substrate for their anode materials, first electroplating a 3-dimensional layer of copper, and then laying tin or silicon on top of that. They achieved fantastic energy density both because they cut the amount of copper in half, and also because of the greatly enhanced energy density of the silicon and tin anode materials. Their devices cycled, were weldable, and because of the high electrode surface area would have fantastic power and rate capability. They weren’t going to be too expensive, either.
Responding to industry demand, they scaled back the idea and decided to market just the copper electroplated separator. This could be coated in a normal way with graphite electrode materials, and so would be a drop-in for battery manufacturers. It had a great rough texture also, which enhanced coating adhesion.
In conversation, I asked Stephanie if they had ever tried vacuum deposition, and suggested they give it a try. With resources stretched thin, she said they hadn’t, so I offered to help. “Let me do the work, and if it works we’ll figure out how to bring it to market.” I had in my mind a potential acquisition or merger of the two companies but thought it best to wait. She agreed, and we exchanged a few emails.
The next part went really fast, as I tend to work on multiple paths in parallel when starting something new. I called some companies that metallize film, and who make metallized film equipment to see about samples. They started arriving immediately. I was invited by a friend to give a talk at George Mason University, and one of the physics faculty there agreed to let a student work on the project. I talked with my friends at Glatfelter, who vacuum metallize paper for labels and decorative applications.
When these samples started coming in, I tinkered: measured conductivity, had some coated with electrode materials, had a few coin cells built. The coin cells worked fine, but when I tried to measure conductivity at a battery voltage, it was impossible to make contact. Ooops, I thought. This may not work. But at least the coin cells were working.
Then I noticed that there was a little hole where I was trying to make contact. Suffering Succotash, Batman—just 4 V could blast a hole in a metal coated plastic!
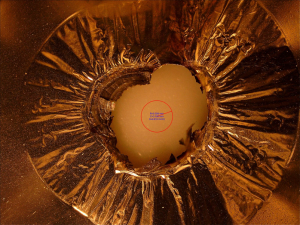
The next experiment sold me: I built a ten-layer cell of just current collectors and separators, using normal foils and plastic separators, but no active materials and no electrolyte. I hooked up alternating foil layers to a power supply set at 4 V. I did a nail penetration test, and the voltage dropped to zero and the current went straight to the limit. Just what you might expect.
Then we built the same stack with metallized foil and our Dreamweaver Gold separator and hooked it up in the same way. When the nail went in, nothing happened. Like the nail wasn’t even there. No measurable spark of any kind. A dozen other experiments like this using scissors, forks, etc. proved what I thought—that this structure just would not support a spark. No spark would mean no cell ignition, and no more lithium ion battery fires.
Somewhere along the way I had done the back of the envelope calculations. How much metal was there? How much was needed for normal cell operation? In a normal cell, there is 8 micron of copper weighing 72 grams/m2, and 15 micron of aluminum weighing 45 grams/m2.
So how much was needed for normal operation? A 20-layer pouch cell might have an internal resistance of 5 milliohms. That means that each layer would be more like 100 milliohms. The metal should be less, maybe 20-40 milliohms/square. With a conductivity of 2.65 x 10-8 ohm-m, this meant we could get by with less than 1 micron total, as 1 micron would give 26.5 milliohms/square, right in our range. In practice, you need less than that, or 400 nm per side on a double-sided coating for a total of 0.8 micron, so back of the envelope got us close.
Here’s the crazy part—we are taking almost 120 grams/m2 of metal down to 6 grams/m2, and adding in only about 20 grams/m2 of plastic, for a total weight savings of about 80%! In a practical cell, this amounts to a 10-20% weight savings, or about 100 kg for a 100 kWh electric vehicle.
A Land War in Asia & Other Classic Blunders
At the same time, I was facing frustration from another source. Over three years I had made a dozen trips to Korea and China and had production cells being made with our separator at a dozen or so major battery and supercapacitor manufacturers. Once we got past the production issues, the battery testing was going very well, and we had been qualified at a couple of different manufacturers for their production cells.
But the big, keep-the-lights-on and fill-the-plant POs never came. I was hosted at seemingly hundreds of fine Korean barbeque and Chinese round-table dinners and lunches, was treated like visiting royalty and had made good friends with our customers. What was I doing wrong?
I looked at the other materials that were prevalent in the market, and stumbled on a couple stories that helped me understand.
3M and NMC
Professor Jeff Dahn at Dalhausie University invented mixed metal oxide cathode materials at the end of the 20th century, with the patent filings coming in 2000 – 2004. This is NMC. The rights to the technology were owned by 3M, and they scaled the technology and launched a business to sell the cathode powder into the battery industry. But the battery companies didn’t buy the powder from 3M. Instead, they got the powder from somewhere else, presumably their LCO powder providers, and began to sell cells in areas where 3M controlled the patents.
In March of 2007, 3M filed two actions naming Sony, Lenovo, Panasonic, CDW, Batteries.com, Hitachi, Matsushita, Total Micro Technologies and Sanyo as defendants in the cases. In essence, they were shutting down the sale of batteries using these materials in areas where they had patent coverage.
By May of 2007, a drumbeat of settlements was being announced. Panasonic and Matsushita settled in May 2007. Sony settled in July, and Lenovo settled in September 2007. Sanyo, Hitachi and CDW all settled in October 2007. Then, 3M began to sell licenses to other suppliers. They never became a giant producer of the powder, but had a very successful licensing business that was eventually sold to Umicore in 2017. Today, NMC amounts to about 30% of the market, and is in all of the electric vehicles except Tesla and ones using lithium iron phosphate, mostly in China.
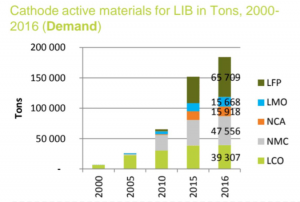
LFP and Ceramic Coated Separators
The story has replayed itself with only subtle variations in two other materials. Lithium iron phosphate batteries were invented by John Goodenough at the University of Texas in 1996, who collaborated with Hydro Quebec. Several companies began to practice variants, including A123, Valence Technology and NTT. At the end of the law suits, a new company, LIFEPo4+C Licensing AG was started to consolidate the intellectual property and distribute the royalties. Material is now made under license by several companies, including Pulead, Aleees, Johnson Matthey, LG and A123. Because there is no patent coverage in China, there are also domestic Chinese companies making the material without paying royalties, but the material cannot be shipped out of China. LFP accounts for about 30% of the cathode market.
The same story is happening in ceramic coated separators. Invented by John Zhang at Celgard to help fix the safety issues inherent with separators that melt and shrink, he coated them with a thin layer of ceramic nanoparticles. Celgard allowed their customers to do the ceramic coating if they used Celgard separators. But some coated separators made by other suppliers, and Celgard launched a parade of law suits with defendants including Sumitomo, LG and others. In 2016, Polypore, which owns Celgard, was sold to Asahi Kesai for $3.2 billion, a multiple of 5.0x revenue and 24.5 x TTM EBITDA. Ceramic coated separators are around 35% of the separator market.
Something BIG
My conclusion is that the lithium ion battery industry will not accept a sole supplier of an important material. As I was learning this, I studied multi-company commercialization efforts of technology, most from the electronics industry, and learned that industry syndicates and consortia are common, including BluRay, HDTV, HDDVD, LTE and 4G.
I had the idea of building a consortium to support a broad supply chain of the materials that make up this new, ultra-safe and light weight architecture consisting of the Dreamweaver separators and the Soteria current collectors. I interviewed several dozen customers, end-users, potential licensees and equipment and material makers, and all of them liked the idea.
The technology can completely eliminate the electrical energy as a source of ignition for battery fires. This means that virtually every battery fire that happens today will not happen with our architecture. Thousands of people, or perhaps millions, could be taken out of danger if this technology is broadly adopted. I began to think about young children in the back of an overturned electric vehicle, unable to get out, but otherwise unhurt. Would I be responsible for whether that vehicle was on fire? Even if this scenario happens only once, I had to make the technology available.
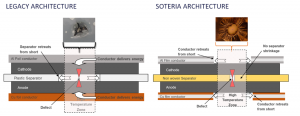
As a serial entrepreneur I have a few rules about naming a company—it needs to be easy to spell, have three or fewer syllables, and not be used in the industry. While looking for a name, I was looking for the word “safe” or “safety” in other languages and stumbled on the word Soteria. “Soteria” was the Greek goddess of safety and means “safety” in Greek. It is also the word used in the New Testament for the salvation offered by faith in Jesus Christ. From the moment I saw it on my computer screen and understood the meaning, it rang true, even though it breaks most of my new-company-name rules.
As of July 2018, Glatfelter has purchased the first license and the consortium—battery innovation group, or BIG—has been formed with an A-list group of initial members including NASA, Daimler, DuPont, DNV-GL, Voith, Ingevity and others. We are up to 18 members, with new ones joining every month, and have been selected as a semi-finalist in the Innostars competition as well as for the Pepperdine Most Fundable Companies. We have engaged Technova to help us found Soteria BIG India, and have other groups helping us form Soteria BIG China and Soteria BIG Europe.
During the Q&A portion of my pitch to Innostars, I was asked how we are going to prevent other companies from copying our technology. “We won’t,” I said. “In fact, we are going to teach the industry how to use the technology. Our plan is to pick honest partners with high integrity and ask everyone to work together, and hopefully the benefits of joining the team will outweigh the benefits of cheating. When people do cheat, we will hire lawyers and sue them to collect the treble damages that are due.” Our royalty rate will amount to 0.5% of the cost of a battery, or about $0.005 for a cell phone, and $25 for an EV. If someone cheats, we will sue them. But can we allow the pursuit of a few dollars to trap someone’s daughter in an overturned car while the batteries are exploding around her? Not on my watch.
Dr. Brian Morin is co-Founder and CEO of the Soteria Battery Innovation Group. He is President and co- Founder of Dreamweaver International, and was formerly founder and CEO of Innegrity. Brian received his Ph.D. and M.S. degrees in materials physics from The Ohio State University, and his B.S. degree in physics from the University of North Carolina. Brian has applied for over 200 US & international patents on subjects ranging from molecular magnetic materials to polymer additives to advanced fibers and battery materials. He can be reached at Brian.Morin@SoteriaBIG.com.