Contributed Commentary by Alex Yeung, Global Business Development Manager, Branson Welding and Assembly at Emerson
July 14, 2021 | In the 25 years since General Motors introduced its EV1 and the 13 years since Tesla’s Roadster hit the streets, all-electric vehicles have come a long way in the eyes of the consumer—and the world. Market acceptance of EVs continues to grow and seems to track closely with continuous improvements in battery technology. Consumers generally want several things: greater energy density for longer range, faster charging, improved safety, and long-term affordability.
Worldwide, battery makers are working hard to develop new technologies to meet these expectations. Ongoing research is driving the development of new separator materials that can prevent dendrite formation and enable practical solid-state batteries. Current battery chemistries continue to advance, with nickel-metal-cobalt (NMC)/graphite chemistry the best option for maximum range, albeit there are questions concerning its cost and reliance on a limited global supply of cobalt. Meanwhile, lithium ferro phosphate (LFP)/graphite chemistry offers a lower-cost alternative for EV applications that do not require the range. And new battery packaging options, such as the innovative cell-to-pack approach, portend weight and space savings that will lead to continued gains in energy density. These and other approaches have driven the peak energy density of commercially available EV batteries up to 260 watt hours per kilogram, and soon will drive it even higher.
In the eyes of the consumer—or the eyes of governments seeking ways to realize a cleaner, cooler and lower-carbon future—the remarkable strides made by battery developers and manufacturers in commercializing reliable and increasingly affordable battery and charging technology can seem routine. But they are not. Each enhancement is the result of intense effort.
For example, many improvements in energy density have resulted from improved assembly methods that incorporate more anode/cathode layers into the confines of existing battery cell designs. These layers, made up of extremely thin metal foils (typically 5 to 8 microns) separated by electrolyte, are the basis of the battery’s ability to charge and discharge electric current. Adding layers provides increased current-carrying surface area and, therefore, boosts energy density and fast-charging capacity.
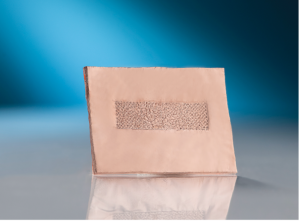
Currently, battery makers can reliably fabricate battery cells with a maximum of about 40 or 50 foil layers. The anode/cathode ends of these fragile foils must be bonded together, typically with ultrasonic foil-to-tab welds, which provide a low-resistance, molecular-level bond. For some time, the solution to adding these layers was quite simple: just boost the energy delivered through the ultrasonic welder. Industry-wide, this approach produced predictable results: a many-layered bond of foils or a metal-to-cable termination—both characterized by high strength and a crisp, discernible weld mark created by the pressure of the weld tooling against the parts. The same equation largely held true for the conductors essential to charging systems. As larger-diameter conductors were needed to handle higher flows of charging current, a boost in welding power was generally the solution for putting them together.
But more recently, as the number of foils surpassed 60 (and 80 or 100 in certain tests), and the surface area (square millimeters) of charging cables has continued to grow, manufacturers found that simply adding more weld power was not working as expected: Conductors, whether many-layered foils or stranded cables, were being damaged. Weld experts determined that damage was occurring because the higher power levels needed to bond thicker or more layered structures were starting to exceed the mechanical capabilities of the typical ultrasonic welders in use. The high-energy welds, when delivered through the cantilever-type actuator arms used on most welders, were causing excessive vibration that led them to lose clamp force and a stable, robust grip on the parts. Thin foil layers shifted during welding, resulting in wrinkles, cracks, or tears, while stranded conductors encountered higher bending and stretching stresses, resulting in strand fatigue and mechanical failures. In both cases, instead of compressing, gripping, and vibrating, the conductors to produce a finished weld, the weld tooling began to lose its grip, allow slippage and damage the parts instead.
Given the huge installed base of ultrasonic equipment serving battery manufacturers, this problem caused concern. If a tried-and-true ultrasonic welding method was not the answer, then what was?
Fortunately, the problem was solved through a combination of manufacturer experience, supplier experimentation and plain necessity. The key to the solution was to use a vertical—rather than horizontal—actuator arm capable of delivering higher clamp force with greater stability on the parts. This “direct press” approach eliminates undesirable actuator stress and vibration, improves tooling “grip” on the parts to be welded and delivers weld energy far more efficiently. With this method, larger welds of 100-plus foil layers or large-diameter stranded cables can now be made using just 30% to 40% as much weld energy as before.
This innovation is just one small example of the many that occur in this industry every day. And it is why I believe that that the effort to produce more powerful, faster-charging batteries will succeed sooner, and in more ways, than many of us thought possible.
Alex Yeung is the global business development manager, Branson Welding and Assembly at Emerson, leading sales, application development and business development for Branson metal welding technology. Yeung holds a B.E. in mechanical engineering from Hong Kong Polytechnic University.