Ty Bowman, Global Battery Market Manager
TE Circuit Protection, a Business Unit of TE Connectivity
In 2010, a metal hybrid PPTC (MHP) technology was introduced to address the rapidly expanding market for high-rate-discharge lithium ion (Li-Ion) battery applications. The MHP arc-less contact technology results in circuit protection devices capable of providing 30 A+ hold currents at voltage ratings over 30 VDC. The MHP devices offer designers a cost-effective, space-saving alternative to conventional battery pack design solutions. This article describes how the latest MHP technology, introduced in 2012, builds upon the previous-generation MHP device family by adding Smart Activation functionality.
New Approach to Battery Protection
Due to advances in Li-Ion technology, smaller, lighter weight and higher-power Li-Ion batteries can now replace nickel cadmium or lead acid batteries previously used in high-rate-discharge battery applications. This trend has resulted in more high-power applications switching to Li-Ion battery technology. This, in turn, has created the need for more robust circuit protection solutions to help ensure battery safety in end-products.
Currently, few protection solutions address high-rate-discharge Li-Ion battery applications, such as power tools, E-bikes, light electric vehicles (LEVs) and standby power applications. Furthermore, traditional circuit protection techniques tend to be large, complex and/or expensive.
MHP technology addresses the design trends in the Li-Ion battery pack market by offering a cost-effective, space-saving circuit protection device. By connecting a bimetal protector in parallel with a polymeric positive temperature coefficient, or PPTC device, the MHP device provides resettable overcurrent protection while also utilizing the low resistance of the PPTC device to help prevent arcing in the bimetal protector at higher currents.
Core Design Concept
During normal operation of the MHP device, current passes through the bimetal contact due to its low contact resistance. When an abnormal event occurs, such as a power tool rotor lock, higher current is generated in the circuit causing the bimetal contact to open and its contact resistance to increase. At this point, the current shunts to the lower resistance PPTC device and helps prevent arcing between the contacts while also heating the bimetal, keeping it open and in a latched position.
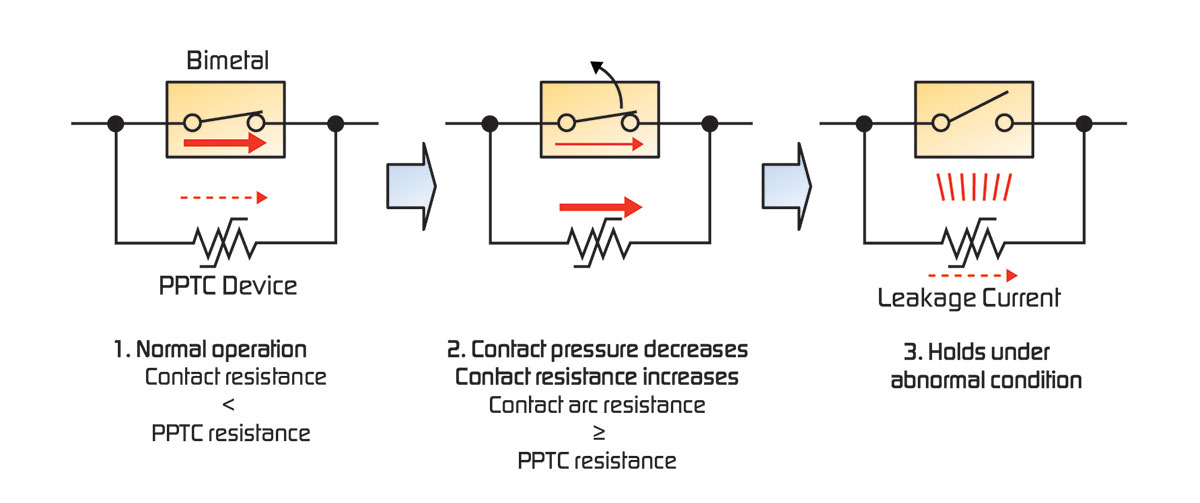
As shown in Figure 1, the activation steps of the MHP
device include:
1. During normal operation, because contact resistance is very low, most of the current goes through the bimetal.
2. When the contact begins to open, contact resistance increases quickly. If the contact resistance is higher than the PPTC device’s resistance most of the current goes to the PPTC device and no, or less, current remains on the contact, therefore preventing arcing between the contacts. When current shunts to the PPTC device, its resistance rapidly increases to a level much higher than the contact resistance and the PPTC device heats up.
3. After the contact opens, the PPTC device starts to heat up the bimetal and keeps it open until the overcurrent event ends or the power is turned off.
A PPTC device’s resistance is much lower than that of a ceramic PTC, which means that even when the contact opens just a small amount, the contact resistance increases only slightly and the current can be shunted to the PPTC device to help prevent arcing on the contacts. Typically, the resistance difference at room temperature between ceramic and polymer PTC devices is in the range of two decades (x10^2), so when higher resistance ceramic PTC devices are combined in parallel with a bimetal they are less effective than MHP devices at suppressing arcs at higher currents.
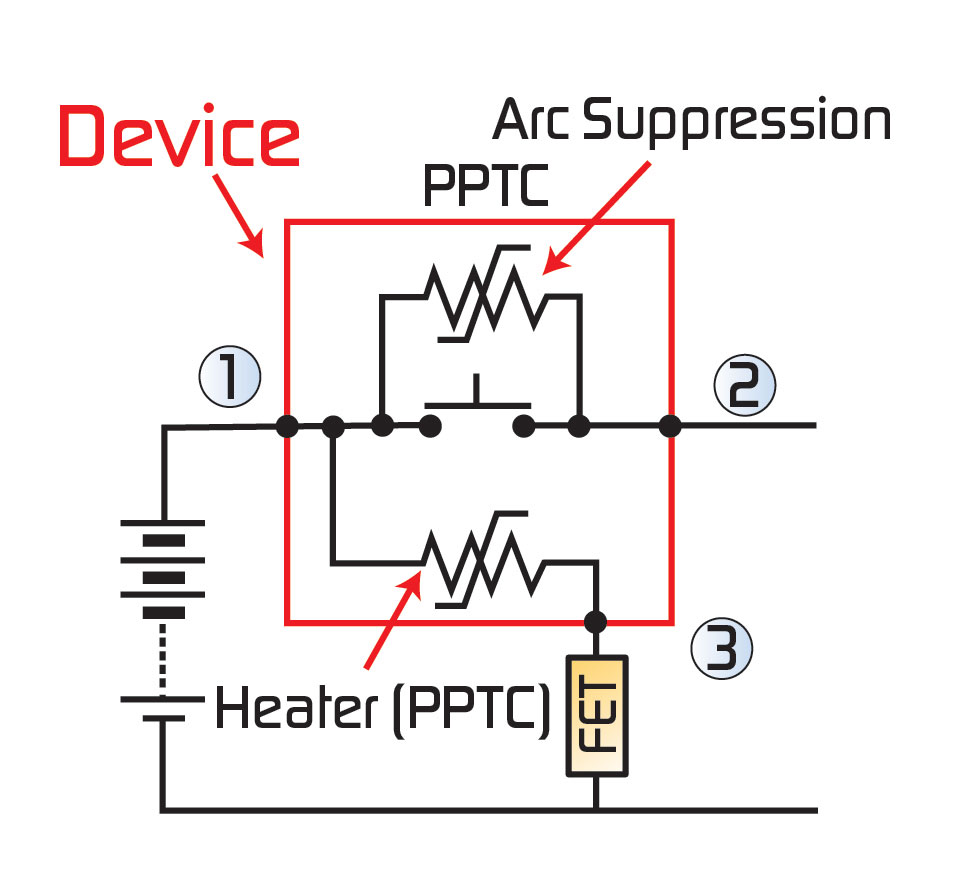
Smart Activation
The latest generation MHP technology, MHP-SA devices, incorporate a third terminal as a signal line for over charge protection. This enables the device to take advantage of the advanced features of the IC that is monitoring various vital functions of the battery. If an abnormality is detected, the IC can send a signal via a low power switch line to activate the MHP-SA device and open the main line, as shown in Figure 2. The activation steps are:
1. The IC monitors the battery system for abnormalities in temperature, current and voltage.
2. The FET (or switch) is ON at an abnormal event (1 → 3).
3. The heater (PPTC) activates and heats bimetal.
4. The contact opens and cuts contact to the main line (1 → 2).
Figure 3 shows an example of the overcharge protection concept and activation steps for the model MHP-SA50-400-M5 (50 A, 400 VDC) device that has a hold current of 50 A on the main line. In this example, the IC monitors individual cell voltage, the FET turns on during an abnormal voltage event, the heater (PPTC) activates and heats the bimetal, and the contact opens and cuts the current to the main line.
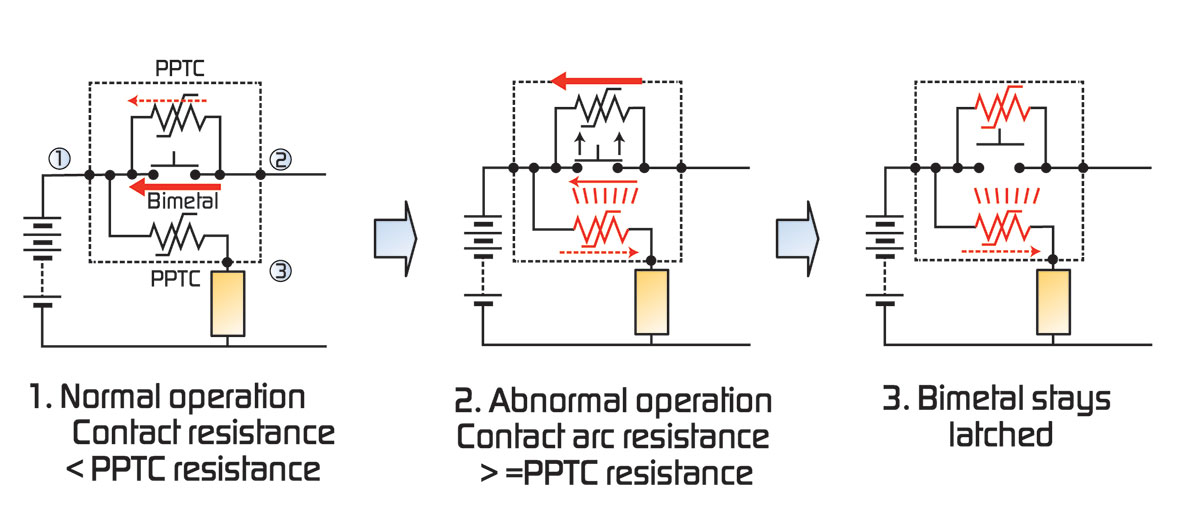
• Main Line Current (1~2): Under normal operation it passes 50 A. Rated at 400 VDC
• Switch Line Current (2~3): Turns on with short circuit current. Rated at 60 VDC
The benefits of the MHP-SA device include:
• Providing over-charge protection in battery packs
• External activation via signal line allows the device to utilize the battery monitoring IC to
detect over-voltage, over-temperature, etc. and activate the device
• Resettable device (e.g., no need to overrate for inrush currents)
• Smaller size and thinner form factor compared to large DC fuses or other breaker devices
• Arc-suppression PPTC design suppresses arc at contacts
• Low power switch line used to open main line (e.g., a lower cost FET can be used)
Decreased Contact Damage – Arcless Contact Technology
Figures 4a and 4b show the current and voltage when using only a bimetal protector. Figure 4a shows the typical results of the open bimetal protector at a rated voltage of 24 VDC/20 A. It opens in 1.28 msec. Figure 4b depicts double the rated voltage of the bimetal protector. A standard bimetal protector arcs under fault conditions and the time from when contact starts to open to welding of the contact (short circuit) is 334 msec.
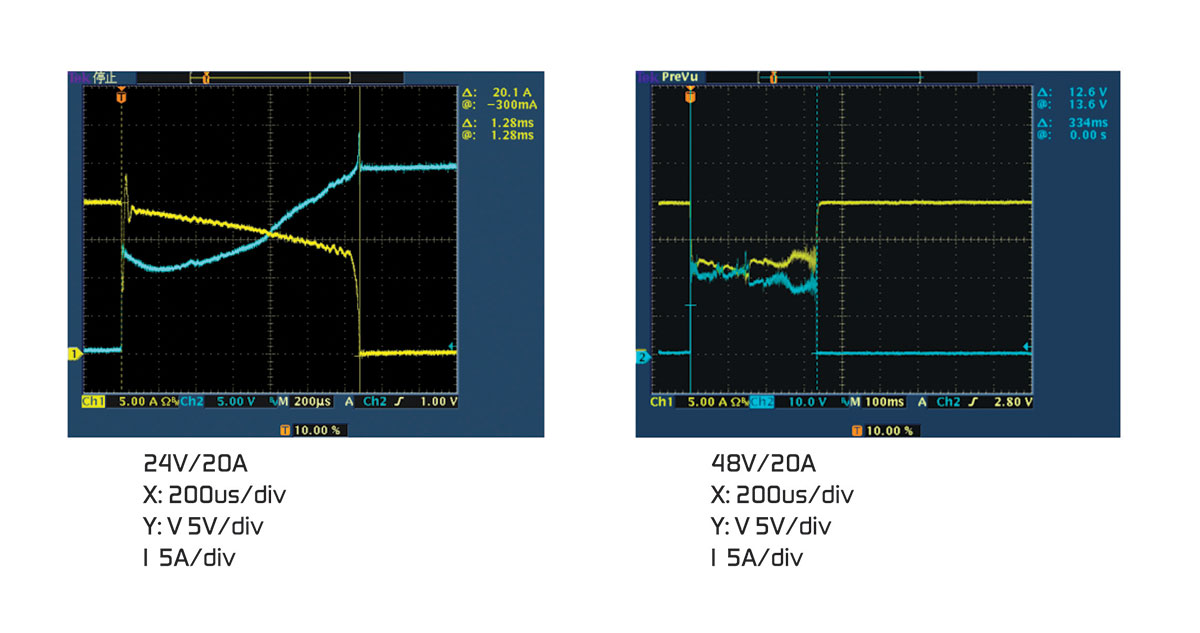
Figures 5a and 5b show the result of combining a PPTC device and bimetal in parallel under a condition in which current is clearly cut off. Figure 5a shows the time lapse between when the bimetal protector starts operating until the PPTC device is fully activated is 6.48 msec. Figure 5b shows the time from the protector operating until current cut off is 4.80 µsec when the applied voltage is two times the rated voltage.
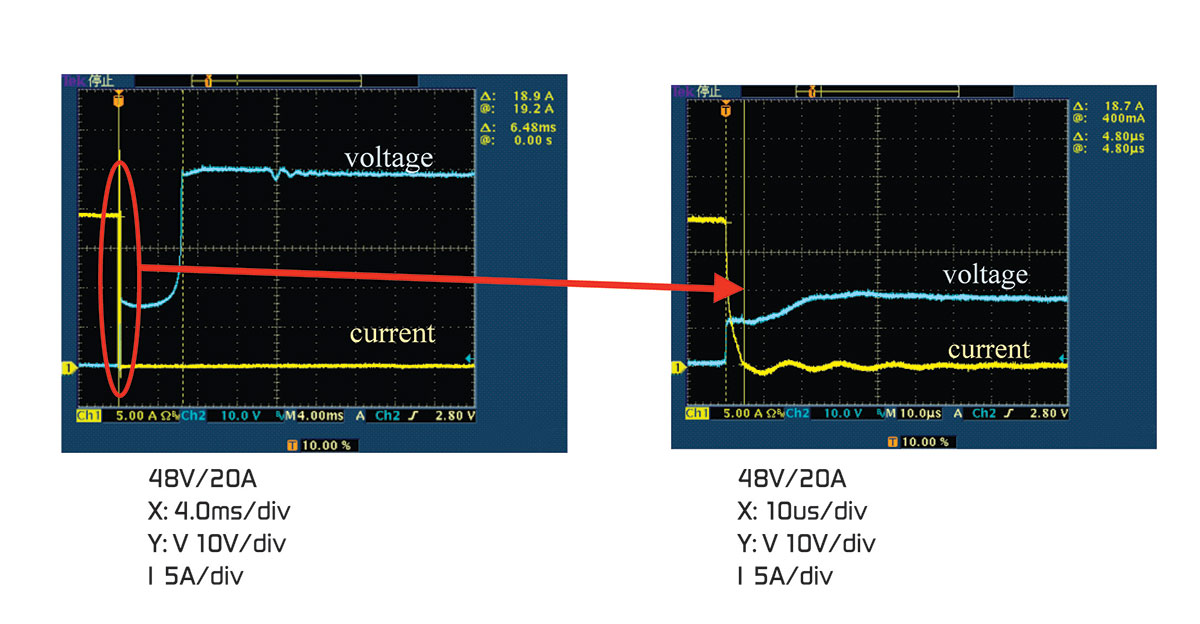
This succession of images demonstrates the smooth transfer from the bimetal protector to the PPTC device with no welding of the protector contacts, and shows how the PPTC device helps protect the contacts from arcing.
The recently introduced MHP-SA50-400-M5 device is housed in an 11.4 mm thick, 71 by 43 mm package incorporating a PPTC device and bimetal protector. This compact device addresses the need for cost-effective safety devices in Li-Ion battery packs.
Application Examples
By selecting PPTCs with different voltage ratings, designs using the MHP-SA device can be configured for a broad range of applications. Device design capabilities with voltage ratings up to 400 VDC and hold current ratings up to 50 A are currently possible, and higher ratings up to 800 VDC are in development.
Several device variations in development offer different size, voltage and hold current ratings that can help meet the protection needs of a broad array of end applications.
• MHP-SA45-42-T (45 A, 42 V): Small size for portable applications such as power tools.
• MHP-SA30-400-M4 (30 A, 400 VDC): High voltage for applications such as Li-Ion battery modules used in a solar power system.
• MHP-SA50-400-M5 (50 A, 400 VDC): High voltage for applications such as Li-Ion battery modules used in smart grid applications or data centers.
Summary
The MHP device provides a rugged, resettable circuit protection solution that offers battery pack designers and manufacturers a method for optimizing space, reducing cost and enhancing safety. The MHP device’s arcless contact technology can be used in Li-Ion battery packs and modules with higher voltage and current ratings; applications that are becoming more prevalent due to advances in Li-Ion technology.
The latest MHP-SA devices incorporate a third terminal for a signal line. This technology allows MHP devices to utilize the smart battery monitoring available in today’s electronics to provide more control over circuit protection in large Li-Ion battery packs and modules for energy storage systems.
MHP and MHP-SA device technology can be configured for various applications, and higher voltage and hold current devices currently in development. Future design considerations include Li-Ion battery protection in applications such as standby power, energy storage systems, as well as non-battery applications such as electric motor protection.
For more information, please visit www.te.com.