Contributed commentary by Isidor Buchmann, CEO & Founder, Cadex Electronics Inc.
Charging a battery is simple but the complexity rises when a parasitic load is present during charge. Depending on battery chemistry, the charge process goes through several stages, and with lithium-ion Stage 1 consists of a constant current (CC) charge that brings the battery to roughly 70 percent state-of-charge (SoC). The cell reaches 4.20V/cell, a common voltage limit for Li-ion, after which Stage 2 continues by applying a constant voltage (CV) charge. The current begins to drop as the battery saturates. Full-charge is reached when the current decreases to typically 0.05C, which is one-twentieth of the rated ampere-hour. Li-ion cannot absorb overcharge and no charge is applied in Stage 3. Figure 1 illustrates typical voltage, current and capacity signatures of the CCCV charge.
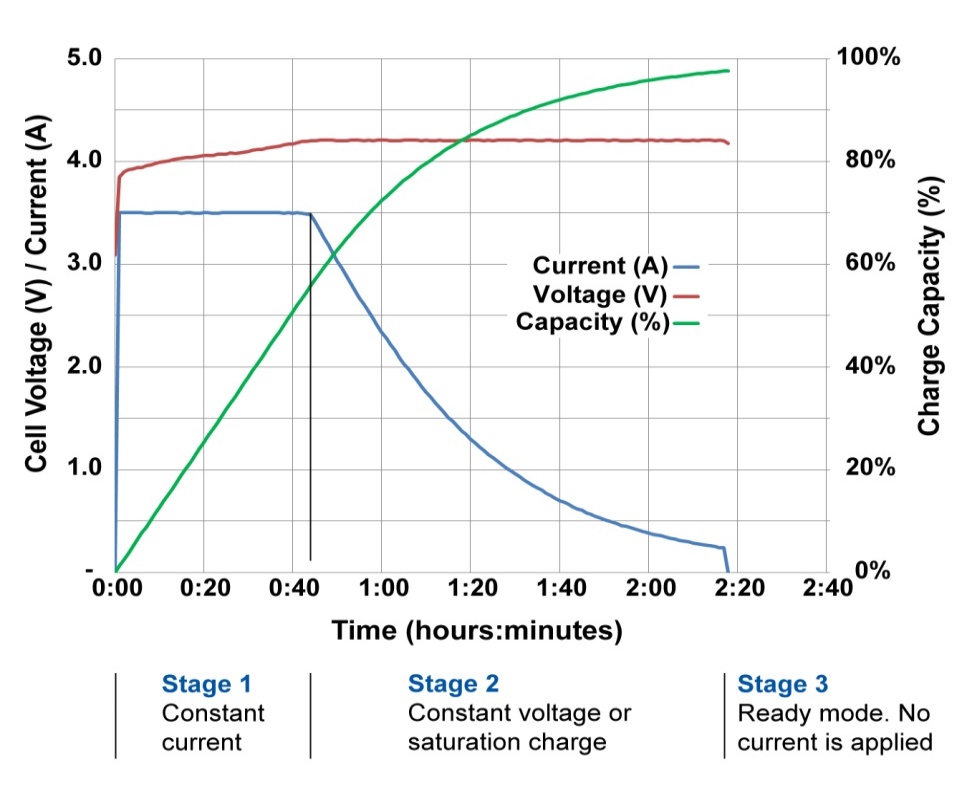
The CCCV method is also used to charge Lead acid with the difference that a float charge is applied in Stage 3 to keep the battery at full charge and to prevent sulfation. Nickel-based batteries receive trickle charge when fully charged to compensate for self-discharge. The Li-ion system is so efficient that excess energy has nowhere to go when the battery is fully charged. Turning the charge current off keeps the battery stable and enables the voltage to neutralize. A continuous float charge, also known as high-voltage-hold, increases the Li-ion battery to above the specified upper cut-offs potential. This would possibly produce gas; possibly cause a breakdown of cell components and probably shorten battery life and compromise safety.
Type of Battery Usage
Battery usage can be categorized into three groups. The most basic is the Detachable Mode where the battery is charged outside the device unaffected by a parasitic load. Applications include mobile radios, power tools, drones, and general instrumentations. This Detached Mode enables the most simplistic charge method because the battery is independent from a device. Most commercial charging chips are designed to operate in this mode.
A growing usage pattern is the Contained Mode in which the battery is charged in the equipment. Smartphone, laptops and some medical devices are examples. The battery is charged in the device by connecting to the grid. The available AC power is divided into charging the battery and operating the device. When fully charged, the battery disconnects from the charger but may from time to time receive a topping charge. This typically occurs when the state-of-charge drops to 93 percent.
The third group is the Attached Mode where the battery is installed in a device. Typical applications are vehicles delivering hotel load and starting the engine. In the Attached Mode, the battery becomes part of an integrated system that is charged during the operation. Some medical, military and industrial devices also operate in Attached Mode providing vital functions. Table 2 summarizes battery usages in different charging environments.
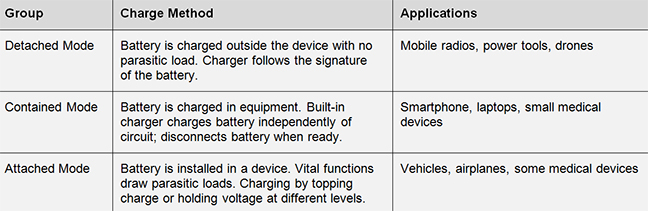
Parasitic Load
The presence of a continuous parasitic load on a battery complicates the charging process. It should be noted that most devices draw some parasitic load but the current is low and may consist of protection circuit for the Li-ion battery, memory back-up or running a clock. This does not distort the charge routine and can in most cases be ignored. However, the parasitic load in the Attached Mode can be high and distort the saturation signature in Stage 2. Such interference in the charging regime requires an alternate full-charge detection mechanism.
Possible solutions are reducing the charge current in Stage 2 for some time, then turning the charge off and applying a topping charge when the state-of-charge drops to 93 percent. Another method is keeping the cell at the 4.20V/cell level. This would be the simplest technique but most Li-ion manufacturers do not approve of this method for safety and longevity reasons. A further option is lowering the charge from the customary 4.20V/cell to 4.10V/cell. This reduces capacity and cell manufacturers consider this viable but are not totally comfortable.
Scientists are studying the behavior of Li-ion at various high-voltage-holds as a function of electrolyte additives and choice of active materials. Unofficial findings show that cycling cells with extended hold times at 4.20V/cell does not lead to lithium plating with quality cells. However lower grade cells could develop high impedance, which can result in Li-plating when held at 4.20V/cell for an extended period of time at elevated temperatures of 40°C.
Keeping Li-ion at high-voltage-hold is a sensitive issue. Few technical papers have been published that suggest how to correctly charge a battery with a parasitic load, nor do battery manufacturers share best practices. It is known that float charging at elevated temperature can cause a breakdown of cell components, which can potentially lead to an electrical short in the cell. Findings reveal that this defect does not necessarily relate to lithium plating that occurs when exceeding the charge voltage or when charging below freezing. Other harmful effects are at work that requires further examination.
Component breakdown can be reduced with electrolyte additives. Each battery manufacturer has its own secret sauce and is hesitant to publish the ingredients. As smoking and lack of exercise affects the health of each person differently, so also is no consistent information available when charging a specific Li-ion system with a parasitic load. There appears to be a lack of information on the effect of high-voltage-hold on Li-ion, especially when operating at elevated temperature and when fast-charging.
Let’s look at lead acid, a system that shares similarities with Li-ion with charging but is more forgiving with overcharge. In Stage 1, lead acid charges to 2.40V/cell. Applying a fully saturated charge at Stage 2 is important to prevent sulfation. Instead of cutting the charge current to zero when ready, Stage 3 lowers the voltage from 2.40V/cell to 2.25V/cell to maintain full-charge. Keeping lead acid at the high 2.40V/cell would cause gassing and promote plate corrosion. Applying a voltage reduction is important especially in stationary applications where the battery is under continuous charge.
The charging system in a vehicle brings the battery to typically 14.40V (2.40V/cell) with no provision to lower the voltage when fully charged. Reducing the voltage to 13.50V (2.25V/cell) on a long road trip would be preferable but lead acid is forgiving and tolerates this condition by receiving rest when the vehicle is parked.
Starter batteries are often replaced with LiFePO (Li-Phosphate) running on the same charging system. Four cells in series produce 12.80V, a similar voltage to six 2V lead acid cells in series. Each of the four Li-phosphate cell tops at 3.60V, which is the correct full-charge voltage. At this point, the charge should be disconnected but the topping charge of the vehicular charger continues while driving.
Li-phosphate is tolerant to some overcharge; however, keeping the voltage at 14.40V for a prolonged time could stress the battery. Time will tell how durable Li-Phosphate will be when operating with a regular charging system programmed for lead acid. Li-phosphate batteries are also being installed in wheelchairs, scooters, golf cars and computers-on-wheels in hospitals. It is wise to assure charger compatibility when replacing lead acid with Li-phosphate.
An aircraft shares similarities with a vehicle in that both systems operate in the Attached Mode. As in a vehicle, the battery in an aircraft can be disconnected once the auxiliary generator provides power. An incident occurred when a nickel-cadmium (NiCd) battery overheated on a Boeing 777 in mid-flight. The circuit breaker was pulled without incident to separate the battery from the system.
Pilots demand that the battery be at full charge at all times. With NiCd, the common on-ship battery of passenger airplanes, this is no problem, but the Boeing 787 Dreamliner is equipped with Li-ion operating in Attached Mode. In 2013 this battery did indeed develop problems but experts say that the onboard battery fires were not caused by incorrect charging but by battery flaws. Whereas the failure rate of a quality Li-ion battery produced by major manufacturers is around 1 in 10 million, the early Boeing 787 batteries had a failure rate of 3 in 800.
In the early 1970s, the National Transportation Safety Board reported several battery incidents per year involving the then new NiCd, but none led to casualties. A redesign eventually made NiCd safe and similar improvements will also be made with Li-ion on board of an aircraft.
One big advantage of Li-ion apart from higher specific energy is their low maintenance. The Boeing engineers did, however, reach out to the automotive sector to learn how large Li-ion batteries are managed in electric vehicles. They discovered that an EV battery has some 50 sensing points for safety; the Boeing 787 had fewer than ten. This shortcoming has now been corrected.
Summary
How should a Li-ion battery be charged with a parasitic load? A solution is high-voltage-hold by applying a float charge in the Attached Mode, but this removes one level of safety redundancy, which concerns battery manufacturers. Should the float charge go out of control, the cell gets overcharged and lithium plating will occur. It is also known that high-voltage-hold at elevated temperature causes a breakdown of cell components. The long-term effects in practical use may not yet be fully understood.
The answer to safely operate Li-ion in the Attached Mode may lay in the choice of electrolyte additives as well as lowering the full charge state. The stress level of Li-ion is lowest between a state-of-charge of 30 and 80 percent. EVs use this preferred SoC bandwidth to achieve extraordinary long battery life, however the packs must be oversized to compensate for the reduced capacity.
Li-ion is optimized for various applications that range from high-energy single cells for consumer products, to sturdy multi-cell configurations for medical, military and mobility use, and to high power cells for power tools. Operating Li-ion in the Attached Mode is a growing market and battery manufacturers will need to take note and deliver a product that will serve this new application.
Isidor Buchmann is the founder and CEO of Cadex Electronics Inc. For three decades, Buchmann has studied the behavior of rechargeable batteries in practical, everyday applications, has written award-winning articles including the best-selling book “Batteries in a Portable World,” now in its fourth edition. Cadex specializes in the design and manufacturing of battery chargers, analyzers and monitoring devices. For more information on batteries, visit www.batteryuniversity.com; product information is on www.cadex.com.