Commentary contributed by Jeff Gelb, Carl Zeiss Microscopy
September 14, 2017 | Batteries are complex systems. From the protective mechanisms in the packaging to the finest details of the active materials, a wide range of structures must work together in order for a battery to function properly. As consumers and government agencies alike demand higher energy densities at lower costs per kwh, optimizing these complex systems is of critical importance to furthering battery technologies. In parallel with optimizing the functionality of the cells, it is equally important to ensure the safe and reliable operation of the battery product, during normal use, storage, or extreme conditions. Addressing these issues requires a full understanding of a battery’s life cycle, from formation through performance, so that root-causes can be identified and modifications to structure and/or chemistry may be made.
In order to predict how a material will perform and, ultimately, fail, the mechanisms of operation must be fully understood. Understanding and optimizing any material system relies on a robust suite of tools, from characterization instrumentation to computational techniques, and batteries are no exception. Characterizing their multi-scale structures involves:
- Light microscopes (LMs)
- Scanning electron microscopes (SEMs)
- Focused ion beams coupled to scanning electron microscopes (FIB-SEMs)
- X-ray microscopes and CT equipment (XRMs and micro-CTs)
- Analytical tools, such as energy dispersive x-ray spectroscopy (EDS) and electron backscatter diffraction (EBSD)
Many researchers have recently turned toward these techniques, combined with conventional electrochemical instrumentation, to better relate battery performance to material microstructures. The combination of these measurements with computer modeling and simulation techniques affords a unique perspective into Li-ion batteries, from the pack to the particle level, and enables new advancements in electrochemistry through conscious material design.
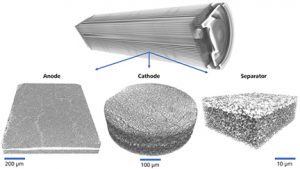
Electrode Layers
Constructing a functioning battery electrode involves many steps, from raw material production to deposition, calendaring, and processing. At each stage, there are possibilities for defects to occur, either as inclusions (chemical defects) or cracks/voids (microstructural defects). Furthermore, the assembly of particle layers results in a complex pore network, responsible for electrolyte transport and facilitating particle lithiation/delithiation as well as SEI formation. The ionic transport rates are believed to be related to electrode porosity, tortuosity, and, thus, effective diffusivity; however, characterizing and enumerating these parameters is a challenging task with conventional instrumentation.
Using a combination of XRM and FIB-SEM-EDS, the multi-scale nature of a battery microstructure may be precisely determined. The X-ray techniques deliver 3D datasets, the integration of which serve as “maps” of the overall microstructure. From these initial surveys, smaller regions of interest may be identified for higher resolution characterization, including microstructural imaging (FIB-SEM) and elemental speciation (EDS). Once this rich, multi-scale dataset is collected, downstream image processing workflows including filtering and binarization/segmentation generate virtual models of the 3D microstructure. These models may be seeded into computer simulation and property prediction routines, which can describe the pore transport and electrical conductivity, in parallel with identifying any production defects captured within the imaging volume(s). The imaging techniques are highly flexible, delivering precise characterizations of anode, cathode, and separator layers alike, as shown in Figure 1.
Battery Assembly
Many issues with commercial batteries may arise once (or after) the product is packaged. Such issues may include compression of the package, expansion of the layers during cycling, or defects introduced through rolling/folding the active material stacks, all of which may lead to short circuits or unpredictable performance. Through a combination of imaging techniques, it is now possible to reveal these features across multiple length scales, including non-destructive examination of the active materials with XRM and high-resolution inspection via sectioning and light- or electron microscopy.
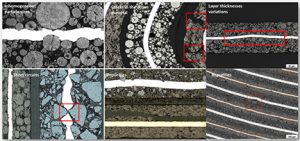
XRM provides a non-destructive means for probing the interiors of materials and devices, meaning that it is capable of providing high-resolution images of battery internals without opening the package. The application of this technique has shown promise for cylindrical cells (e.g., 18650s), pouch cells, and button/coin cells alike. A unique advantage of the XRM approach is the ability to collect images at hierarchically higher resolutions, in order to locate regions exhibiting signs of issues, navigate to those regions, and enlarge them with better feature recognition. In so doing, the structures are characterized across multiple length scales without any physical manipulation, ensuring confidence in the results and delivering an accurate dataset reflective of the specimen microstructure.
Light microscopy has a rich history of application to battery failure analysis and R&D studies alike. This is due, in part, to the wide availability of LMs, the variable resolutions they provide, and the ease of capturing color images in real time. In fully packaged batteries, the challenge in optical characterization is the need to open the battery to expose the region(s) of interest (ROIs). Recently, procedures have been developed where cylindrical and prismatic cells may be carefully sectioned and polished (leveraging an intermediary embedding routine), then imaged with high resolution to reveal the microstructure, as shown in Figure 2. These imaging techniques have been coupled with trainable data analysis routines, ultimately delivering a “map” of defects and a so-called “worst picture gallery” for the user. Combining this procedure with an initial XRM inspection yields a unique workflow for non-destructively mapping the overall battery assembly, then guiding the sectioning system and light microscope to strategically-identified ROIs.
Microstructure Evolution
In addition to cell fabrication and battery assembly, it is well known that batteries change at a microstructural level when operated. These changes may be as simple as a modest volumetric expansion of the active particles, or as complex as the development of cracks/voids/defects as a result of electrochemical cycling. The expansion of the particles may change the pore connectivity and re-route the flow/wetting of electrolyte, while any cracks that develop as a result of large particle expansions may provide new, unintentional pathways for Li-ion transport. At the same time, simply understanding the changes that occur from the particle scale to the full pack helps to better describe the operation of a battery, which may assist in better designing new microstructures and/or revising the existing understanding of how a battery evolves over time.
Microscopy offers a unique solution for characterizing microstructure evolution, capitalizing on the non-destructive nature of XRM and high-resolution capabilities of LM and SEM/FIB-SEM. A specimen may be imaged in one state, treated with some conditions (e.g., aged/cycled or exposed to mechanical/thermal load), and then imaged again, producing a multi-dimensional (3D-4D) dataset capturing the changes within the microstructure. Using advanced computational tools, such as digital image correlation (DIC) or digital volume correlation (DVC), the microstructure changes may be quantitatively determined, in terms of spatial displacement or mechanical strain, highlighting “hotspots” where failure is most likely to initiate.
Digital Design: Putting It All Together
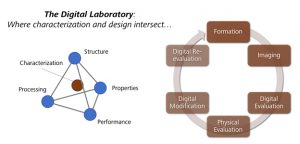
While characterization projects are undoubtedly interesting, few people are in the business of purely understanding battery microstructures or evolutionary dynamics. The goal of the various characterization projects is often, in the end, to design and construct a product that performs differently from competitive or past products. To do this, the additional tooling of computational resources is required, to form the images into models and predict performance in the digital domain.
With modern computer simulation environments, parameters such as effective diffusivity and tortuosity may be predicted, as well as electrical, thermal, and mechanical properties. Given battery microstructure data as input, a researcher may understand how a particular battery was formed and changes; with this understanding in hand, the researcher may then begin altering the chemistry and/or microstructure in the digital realm, using the simulation engine to predict the performance properties. This design loop may be iterated until the optimal parameters are achieved, at which point a new product may be developed and the characterization process repeated. This so-called “digital laboratory” concept, shown in Figure 3, may thus provide dramatically increased development efficiencies, as new and costly-to-develop microstructures may be tested without ever having a need to be physically formed. Simulation engines capable of performing this analysis are now routinely available, from commercial products to freeware packages.
Summary
The immense complexity of Li-ion batteries presents a challenging characterization task to development scientists and engineers. From cycle life characteristics to calendar life behavior, understanding the properties of batteries is critical to designing a successful product. Leveraging a unique suite of instrumentation, including microscopy and spectroscopy equipment along with commercially-available computational tools, this complexity may be simplified across a range of features spanning a range of length scales. Formation and packaging results may be characterized in 2D and 3D using light-, electron-, and X-ray microscopy, and 3D to 4D microstructure evolution may be tracked as the battery operates or is exposed to varying conditions. Using the information achieved through characterization, a new technique of digital material design is now available, which is poised to significantly increase the speed and efficiency of material development by using microscope data as input. The combination of all of these approaches creates new opportunities for scientists and engineers to contribute to the furthering of Li-ion technology, addressing market needs of today while preparing for the demands of tomorrow.
References
- Gelb et al., “Multi-scale 3D investigations of a commercial 18650 Li-ion battery with correlative electron- and X-ray microscopy.” Journal of Power Sources 357 (2017).
- Hafner et al., “The Materialographic Preparation and Microstructure Characterization of Lithium Ion Accumulators.” Practical Metallography 49 (2012).
- Shearing et al., “Exploring electrochemical devices using X-ray microscopy: 3D microstructure of batteries and fuel cells.” Microscopy & Analysis (2013).
- Weisenberger et al., “Multi-scale characterization of a lithium ion battery cathode material by correlative X-ray and FIB-SEM microscopy.” Microscopy & Analysis 139 (2015).
- Yufit et al., “Lithiation-induced dilation mapping in a lithium-ion battery electrode by 3D X-ray microscopy and digital volume correlation.” Advanced Energy Materials 4 (2014).
Jeff is a senior applications engineer at Carl Zeiss Microscopy, focused on workflow development for multi-length scale correlative microscopy. After graduating from UC Santa Barbara in 2005, he began working with advanced X-ray instrumentation and quickly became interested in applying these techniques to studies of electrochemical energy storage and conversion devices. Jeff completed a master’s degree in materials engineering in the spring of 2017 at San Jose State University, where he developed a research methodology for characterizing microstructure evolution in commercial Li-ion batteries. He is excited about the future of electrochemical devices and maintains an interest in supporting this through the development of imaging and computational routines.